Exploring the Versatility of Dip Molding Materials in Business
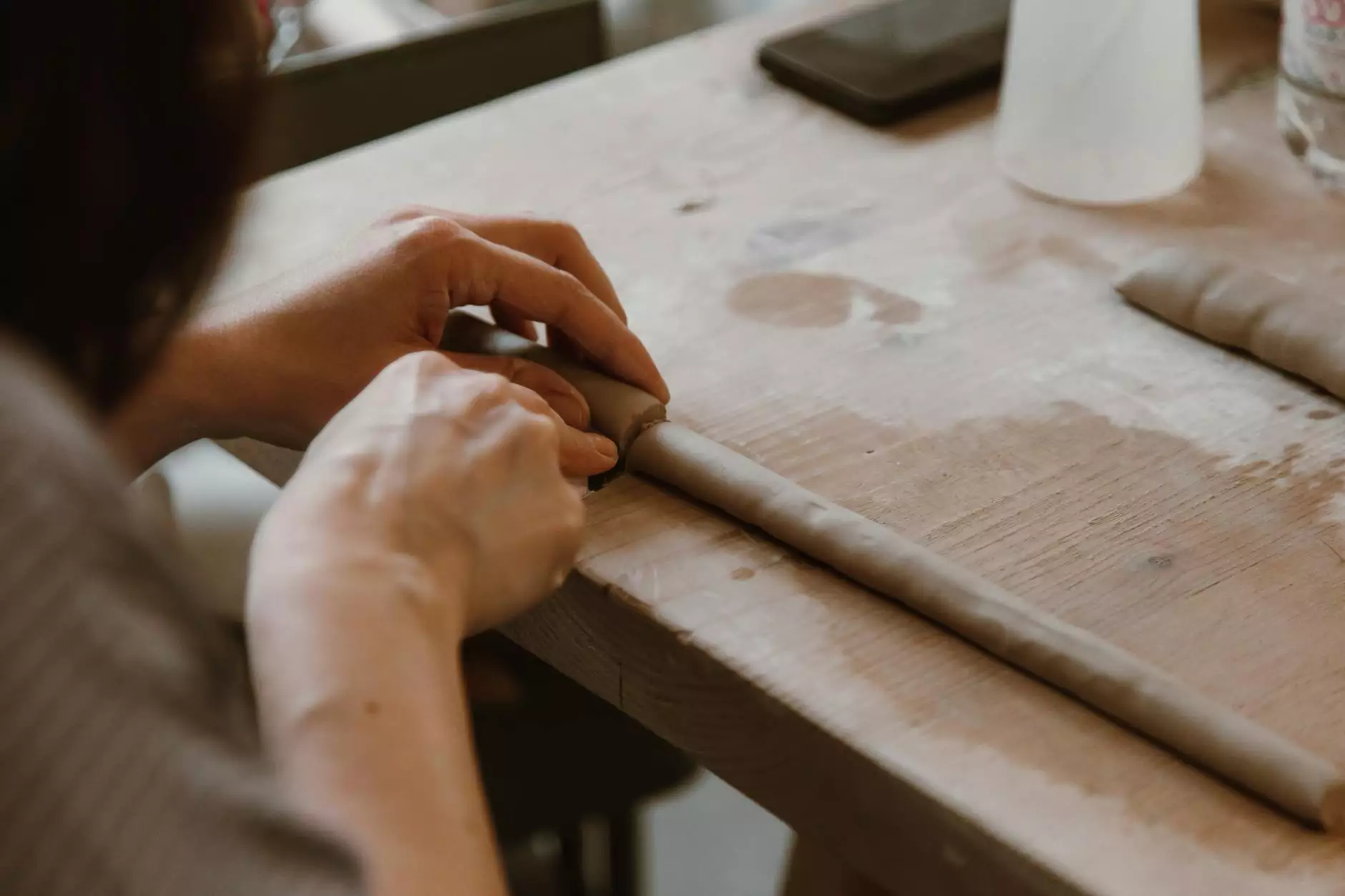
Understanding Dip Molding: A Brief Introduction
Dip molding is a manufacturing process that involves the coating of an object with a polymer material to create a protective layer or an ergonomic grip. This technique is widely popular in various industries, particularly in electronics and medical supplies. The flexibility and adaptability of dip molding materials make them an ideal choice for businesses seeking innovative solutions.
The Significance of Dip Molding in Electronics
In the electronics industry, dip molding materials play a crucial role in the production of various components. These materials offer several benefits that enhance product performance and user experience:
- Durability: Dip molded components are known for their robust nature, providing adequate protection against environmental factors.
- Insulation: The coated products effectively insulate electrical components, preventing short circuits and prolonging the lifespan of the gadgets.
- Customization: Businesses can choose from a variety of colors, textures, and materials, ensuring that their products meet specific aesthetic and functional requirements.
- Cost-Effectiveness: Utilizing dip molding can significantly reduce production costs while maintaining high-quality standards.
Applications of Dip Molding Materials in Electronics
The applications of dip molding materials in the electronics sector are vast, ranging from protective coverings to ergonomic grips. Here are some examples:
- Wire and Cable Coatings: Dip molding creates a protective layer around wires and cables, ensuring they are safe from wear, tear, and environmental damage.
- Switch Covers: A dip molded switch cover not only improves the aesthetic appeal but also adds a layer of protection against dust and moisture.
- Consumer Electronics: Items like remote controls and mobile devices benefit from dip molded grips, enhancing user experience.
The Role of Dip Molding in Medical Supplies
The medical supplies industry has seen remarkable advancements thanks to the application of dip molding materials. The unique properties of these materials make them indispensable in ensuring the safety and functionality of medical devices.
Key Benefits of Dip Molding in Medical Applications
- Biocompatibility: Many dip molded materials are designed to be biocompatible, making them suitable for medical usage directly in contact with patients.
- Ease of Sanitization: The smooth surface finish of dip molded items allows for easier cleaning and sterilization, a critical requirement in healthcare.
- Precision and Consistency: The dip molding process allows manufacturers to produce components with a high degree of precision, which is essential in the medical field.
Applications of Dip Molding Materials in Medical Supplies
The versatility of dip molding materials extends to a wide array of applications within the medical sector:
- Protective Covers: A common use is for protective covers on medical instruments, ensuring hygiene and safety.
- Handles for Surgical Tools: Ergonomically designed grips for surgical instruments enhance user handling, providing better control during procedures.
- Drug Delivery Systems: Dip molded components are used in various drug delivery systems, including inhalers and auto-injectors.
Innovative Materials Used in Dip Molding
The choice of material is critical in the dip molding process, as it directly impacts the quality and application of the finished product. Several types of materials are commonly employed in dip molding:
- Polyvinyl Chloride (PVC): Known for its versatility and cost-effectiveness, PVC is widely used in dip molding.
- Polyurethane (PU): This material offers excellent elasticity and is often utilized for grips and cushioning.
- Silicone: Noted for its biocompatibility, silicone is frequently used in medical applications.
Environmental Considerations in Dip Molding
As businesses become increasingly aware of their environmental impact, the selection of dip molding materials also takes sustainability into account. Eco-friendly materials and practices are gaining traction among manufacturers, enhancing the appeal of dip molding as a green solution.
The Move Towards Sustainable Dip Molding
Companies are now focusing on sustainable materials and more efficient production processes that reduce waste. Innovations in biodegradable polymers and recycling capabilities are quickly changing the landscape of dip molding, making it more attractive for environmentally-conscious businesses.
The Future of Dip Molding in Business
The future of dip molding materials in various industries looks promising. As technology progresses, we expect to see enhancements in material properties and processing techniques, leading to even greater application possibilities.
Potential Technological Advancements
Industries like electronics and medical supplies are likely to benefit from developments in automation and 3D printing, potentially reducing hard costs and improving quality control. We can also foresee new materials that combine the best aspects of existing polymers for specific industry applications.
Conclusion: Embracing the Power of Dip Molding Materials
As we navigate through evolving landscapes in the electronics and medical supplies industries, businesses must embrace the limitless potential that dip molding materials provide. The combination of durability, biocompatibility, and customization empowers manufacturers to create innovative products that meet and exceed consumer expectations. As we continue to innovate and prioritize sustainability, the use of dip molding will undoubtedly solidify its role as a transformative manufacturing process for the future.