Unlocking Business Potential with Silicone Rubber Injection
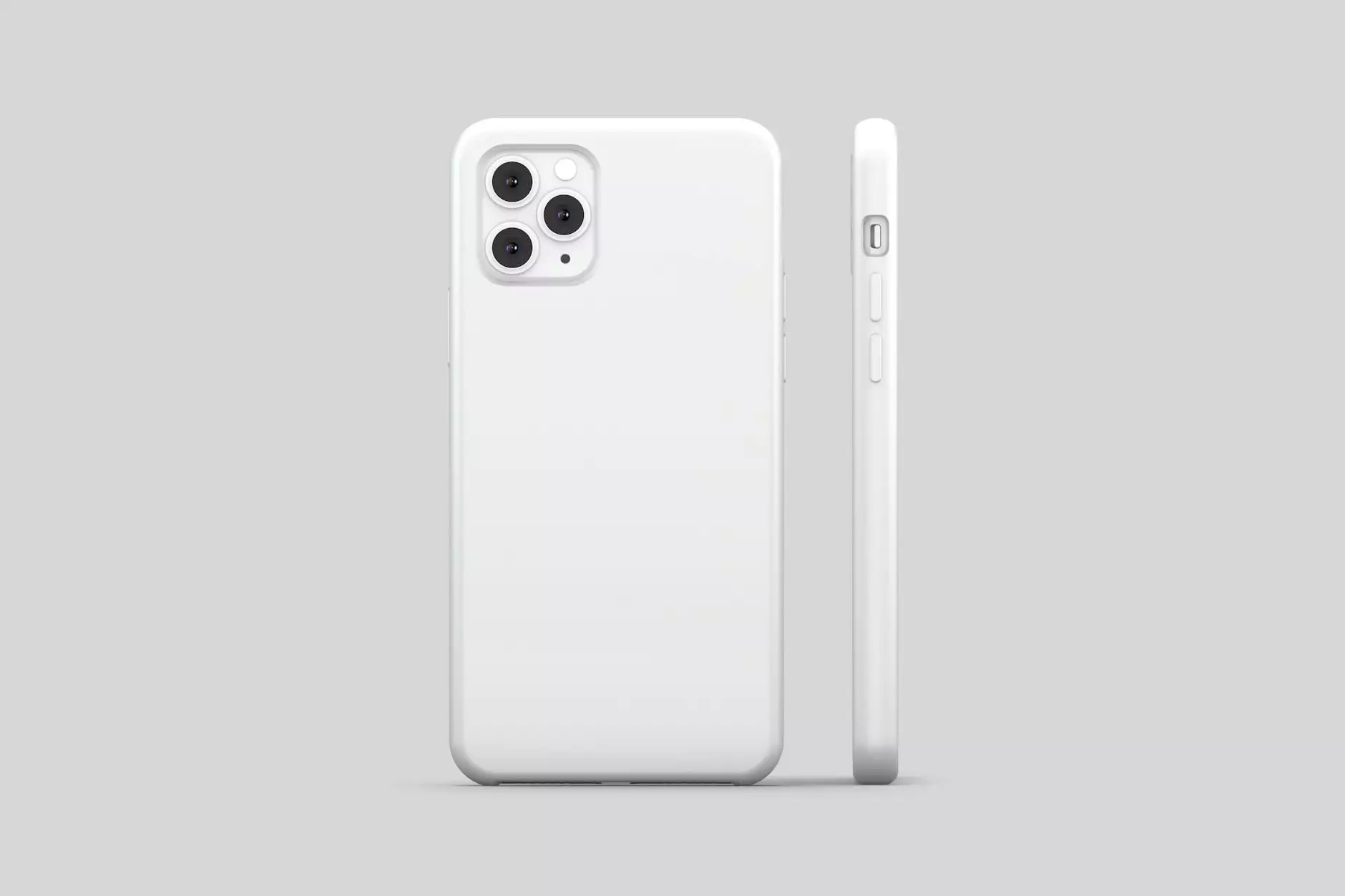
Silicone rubber injection is a transformative process that has changed the landscape of manufacturing across various industries. This advanced technique allows businesses to produce high-quality silicone components that are vital for the functioning of electronic devices and medical supplies. As we dive deeper into this topic, we will explore the benefits, applications, and technical intricacies of silicone rubber injection.
Understanding Silicone Rubber Injection
Silicone rubber injection refers to the method of injecting liquid silicone rubber (LSR) into a mold to form precise and durable parts. This process is widely recognized for its ability to create complex shapes with high precision and minimal waste. Engineers and manufacturers prefer this method due to the numerous advantages it offers, including:
- High efficiency: The injection process allows for rapid production runs, making it ideal for large-scale manufacturing.
- Reduced waste: The precision of the injection process minimizes excess material and scrap.
- Enhanced product performance: Silicone rubber's inherent properties such as heat resistance, flexibility, and durability make it suitable for challenging applications.
- Customization: The formulation of silicone rubber can be tailored to meet specific performance requirements.
The Role of Silicone Rubber Injection in Electronics
The electronics industry has significantly benefited from silicone rubber injection. This innovative method allows manufacturers to produce components with the following characteristics:
1. Sealing and Protection
Silicone rubber is widely used in electronic devices due to its excellent sealing properties and resistance to moisture, which protects sensitive components from damage. Silicone rubber injection enables the production of highly effective seals and gaskets that ensure durability and performance in devices.
2. Insulation and Thermal Stability
In electronics, thermal management is crucial. Silicone rubber retains its physical properties across a wide temperature range, making it an excellent choice for thermal insulation. The injection technique ensures that thermal pads and casings achieve optimal thermal performance, which is essential for maintaining the functionality of electronic components.
3. Versatile Design Options
The flexibility of silicone rubber enables the creation of complex geometries and intricate designs. This is particularly important in modern electronics that often require lightweight yet robust materials. With silicone rubber injection, businesses can design products that are both aesthetically pleasing and functional.
Enhancing Medical Supplies with Silicone Rubber Injection
In the medical field, the need for safe, reliable, and high-quality materials is paramount. Silicone rubber injection has risen to this challenge by offering the following advantages:
1. Biocompatibility
Silicone rubber is known for its biocompatibility, making it an ideal choice for medical devices and supplies. Silicone rubber injection allows manufacturers to produce components such as seals, tubing, and molds that come into contact with bodily fluids safely.
2. Durability and Longevity
Medical devices must withstand rigorous usage and sterilization processes. Silicone rubber exhibits exceptional durability, ensuring that products manufactured through silicone rubber injection can endure repeated sterilization and other harsh conditions without degrading in performance.
3. Precision Engineering
With the high level of precision that silicone rubber injection offers, manufacturers can create intricate components that fit together seamlessly. This is crucial in medical applications where the performance of devices can be life-saving.
Technical Insights into Silicone Rubber Injection
The process of silicone rubber injection involves several key steps that ensure product quality and consistency. Understanding these steps can help businesses make informed decisions about their manufacturing processes:
1. Material Preparation
The first step involves preparing the silicone rubber material. This includes mixing the silicone base with additives to enhance its properties as per the intended application. Factors such as hardness, color, and specific mechanical properties are defined during this stage.
2. Mold Design and Construction
Creating an efficient mold is critical for successful silicone rubber injection. Designers must pay attention to aspects like draft angles, venting, and cooling channels to ensure the smooth flow of silicone into the mold and facilitate easy part removal after injection.
3. Injection Process
The next step is the actual injection. Liquid silicone is heated and injected into the mold cavity under high pressure. The curing process begins immediately, allowing the silicone to form the precise shape of the mold.
4. Post-Processing and Quality Control
After the silicone parts are formed, they are cooled and ejected from the mold. Comprehensive quality control checks are conducted to ensure that all parts meet the required specifications. This step may involve testing for dimensional accuracy, strength, and functional properties.
Market Trends and Innovations in Silicone Rubber Injection
As industries evolve, so do the techniques involved in silicone rubber injection. Here are some emerging trends and innovations:
- Advanced Materials: New formulations of silicone rubber with enhanced properties are being developed, expanding the potential applications in diverse industries.
- Automation and Industry 4.0: The integration of automation and smart technology is revolutionizing the silicone rubber injection process, leading to increased efficiency and reduced costs.
- Sustainability: With a growing emphasis on sustainable manufacturing practices, companies are exploring eco-friendly silicone materials that minimize environmental impact.
Conclusion: The Future of Silicone Rubber Injection
In conclusion, silicone rubber injection is a vital process that supports the production of high-quality components in critical industries like electronics and medical supplies. As we move forward, innovations in technology and materials will continue to enhance the capabilities and applications of silicone rubber injection. For companies like Nolato, leveraging this advanced manufacturing technique can not only improve product quality but also provide a competitive edge in a rapidly evolving market.
Call to Action
To learn more about how silicone rubber injection can benefit your business, visit Nolato today. Discover innovative solutions tailored to your needs and stay ahead in your industry!